|
 |
公司新聞 ->球閥閥桿斷裂技術分析 |
球閥閥桿斷裂技術分析 |
點擊次數:2260 更新時間:2014-11-15 |
|
管線球閥是輸油輸氣管線中*的控制介質元件。某單位使用的一臺進口管線球閥,在項目現場發生了閥桿斷裂事故,導致此臺閥門無法正常使用,委托三精閥門進行維修。為了找到閥桿斷裂的主要原因,特此進行了以下分析。 閥桿斷口位于O形圈槽與臺階的過渡處,斷口面比較平整(見圖1)。閥門經解體后發現:球面有明顯的劃痕,并且有多處坑窩(見圖2);閥座上的O形圈已損壞,存在長約8mm的缺口(見圖3)。 圖1 閥桿斷口形貌
圖2 球體損傷部位 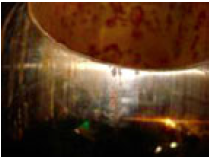
圖3 閥座組件 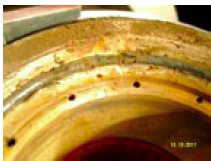
1.過程分析 經解體后得知:此閥門結構為雙向閥座密封固定式球閥,主要由閥體、左右連接體、閥桿、上下支撐板、球體、密封圈、執行機構等組成;密封副由閥座組件上的O形圈與球體球面構成;球體由上下兩個支撐板支撐,通過旋轉執行機構帶動閥桿轉動,從而實現球體的90°旋轉,并通過進出口兩端閥座與球體的密封,實現接通和截斷介質的目的。 這種結構形式的閥門特點是:閥門為筒狀體、固定球結構,閥座采用雙座雙向自密封結構,同時有預緊彈簧,保證密封可靠和自動泄放腔中過高壓力的功能;閥門內置有支撐板,球體通過上下支撐板固定于閥腔之中,大大減小閥桿的受力情況。當閥門在正常工作時,介質的密封力通過支撐板作用到連接體上,使得閥桿承受扭矩很小。 2.理化分析及無損檢測 (1)化學成分用光譜分析儀進行光譜分析,結果參見表1。 表1 閥桿材料化學成分(質量分數) (%)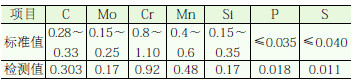 從以上數據分析可以得知:閥桿的材質符合ASTMA322對4130材料的要求。 (2)力學性能試驗斷裂閥桿加工成拉伸試樣,在WE—60型材料試驗機上進行拉伸試驗,試驗結果見表2。 表2 閥桿材料力學性能試驗數據 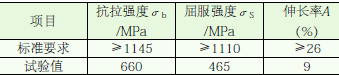
從以上試驗數據可以得知:閥桿的力學性能是不達標的。為了探究力學性能偏低的原因,特此進行了微觀組織分析。 (3)微觀組織分析取樣部位為閥桿斷裂面,金相觀察縱截面金相組織為珠光體與鐵素體(見圖4),而且呈連續帶狀分布,帶狀組織達到5級(按GB/T13299—1991C系列評級標準)。組織中鐵素體晶界清晰可見,珠光體帶寬窄不一,見圖5。 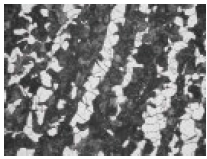 圖4 閥桿截面金相組織100× 圖5 淬火+回火后試件金相形貌500× 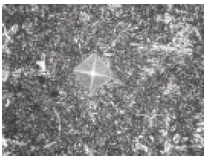
從圖4明顯看出:鐵素體和珠光體呈帶狀交替分布,呈現出較為明顯的帶狀組織,內部組織極不均勻。低合金鋼經調質處理后,內部應分布較為均勻的回火索氏體組織。圖5為試樣經合理工藝進行調質處理的金相組織。 (4)表面硬度檢測閥桿在HB—3000型布氏硬度試驗機上檢測硬度,其表面硬度190~207HBW,明顯偏低。 (5)無損檢測分別對斷裂閥桿按JB/T4730—2005的規定進行了磁粉和超聲波無損檢測,結果顯示:表面及內部無超標缺陷。 3.扭矩及零件尺寸檢測 (1)扭矩檢測重新加工閥桿并組裝后,對事故閥門進行了扭矩測試,結果見表3。 表3 閥門扭矩測試數據 
閥門的啟閉扭矩是隨著壓力的增加而不斷增大的,當壓力達到公稱壓力時,閥門的啟閉扭矩為300N•m,折算到閥桿上的扭矩值為2704N•m。經計算,設計扭矩應為270N•m左右,實際操作扭矩遠大于設計扭矩。為了進一步找到扭矩劇增的其他原因,特此對此閥門的關鍵零件進行了尺寸檢測。 (2)零件尺寸檢測閥門解體后,用三坐標測量儀分別對支撐板、閥體與連接體組件等關鍵零部件進行尺寸檢測,數據見表4。 表4 閥門關鍵零部件尺寸檢測數據 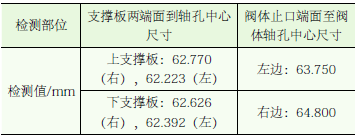
對檢測數據進行分析得知,支撐板端面與連體端面存在較大間隙。上支撐板左邊間隙為1.53mm,右邊間隙為2.03mm;下支撐板左邊間隙為1.36mm,右邊間隙為2.17mm。 若支撐板端面與連接體止口端面間隙過大,則在介質力的作用下,支撐板會發生移動,將壓緊力傳遞到閥桿上,這樣會使閥桿承受很大的扭矩和剪切力。實踐證明:支撐板端面與連接體止口端面之間間隙為0.2~0.5mm時較為適宜。而此臺閥門支撐板與連接體止口端面的間隙遠超過0.5mm,在介質力的作用下,閥桿會承受較大的扭矩。 4.結語 造成此臺管線球閥閥桿斷裂的主要原因有:支撐板端面與連接體止口端面之間存在過大的間隙,尺寸超差;閥桿材料的熱處理工藝不當,導致閥桿的強度、硬度均低于標準值。 |
|
|
|
|
|
|
|
|
|
|
 |
|
 |
|
|